Tag Archive for: CNC machining
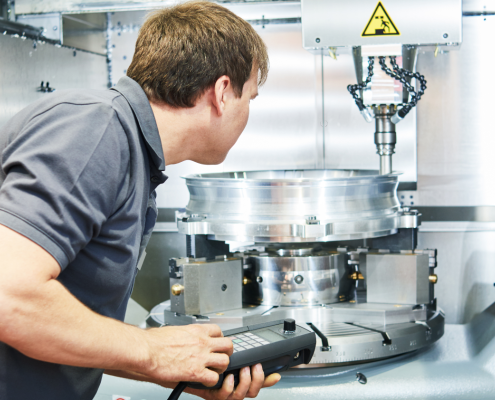
How Metal Presswork, Fabrication, and Machining Work Together in Manufacturing
/
0 Comments
Manufacturing is a highly complex process that requires a combination…
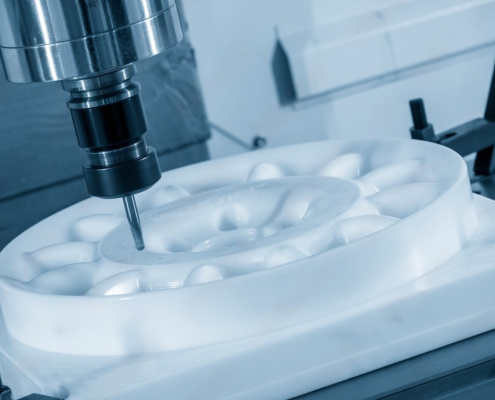
What Makes CNC Machining Ideal for Prototyping and Mass Production?
CNC machining has become a cornerstone of modern manufacturing,…
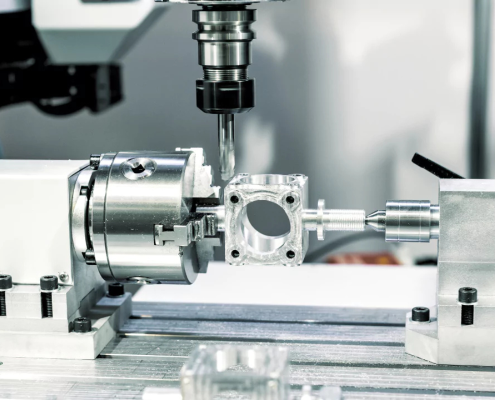
Why CNC Machining Remains a Core Tool in Modern Manufacturing
In the fast-paced world of modern manufacturing, the tools and…
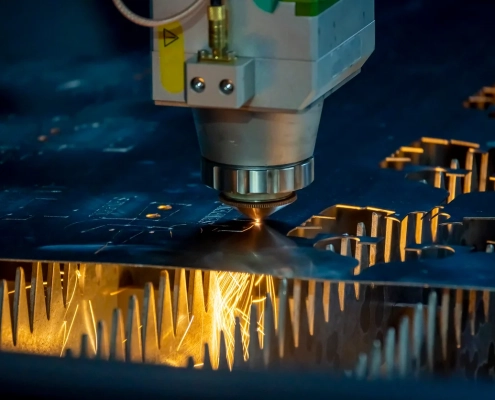
How to Get Accurate CNC, Laser Cutting, and Fabrication Quotes
When you’re undertaking a custom manufacturing project, whether…
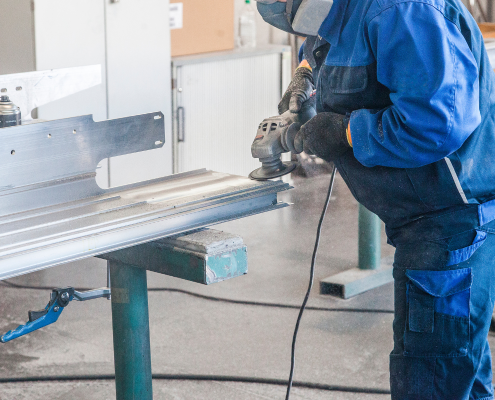
Metal Fabrication Methods Comparison : Choosing Between Welding, Presswork, and Machining
When working on a metal project, choosing the right fabrication…
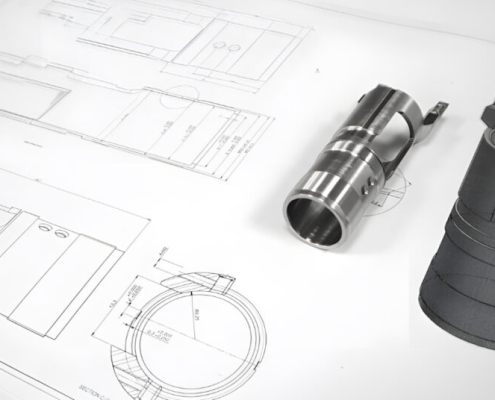
How to Design Parts for CNC Machining: A Beginner’s Guide
Designing parts for CNC machining isn’t just about creating…
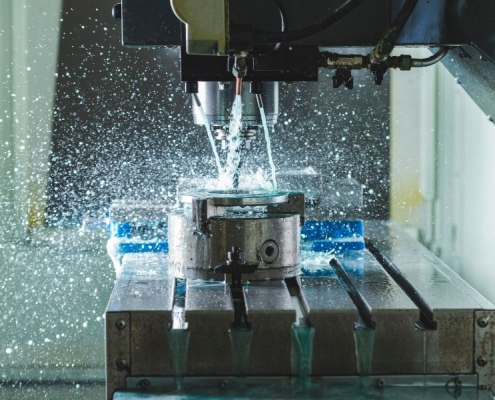
CNC Machining vs Traditional Machining: Which is Right for Your Project?
When you start a manufacturing project, one of the most important…
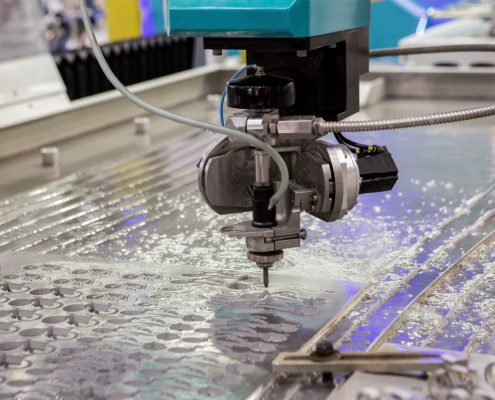
CNC Machining vs 3D Printing: Which One Should You Choose?
When it comes to making parts, two of the most popular options…
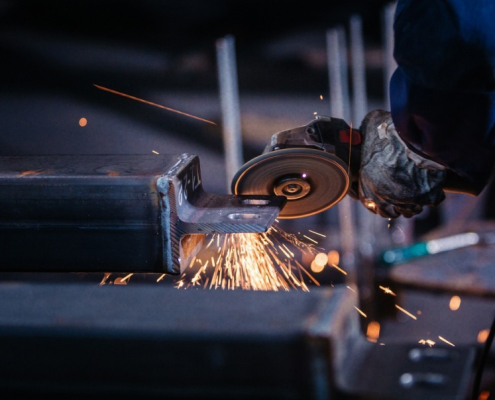
Advantages and Role of Fabrication in Manufacturing
We live in a world built by manufacturing. From the cars we drive…
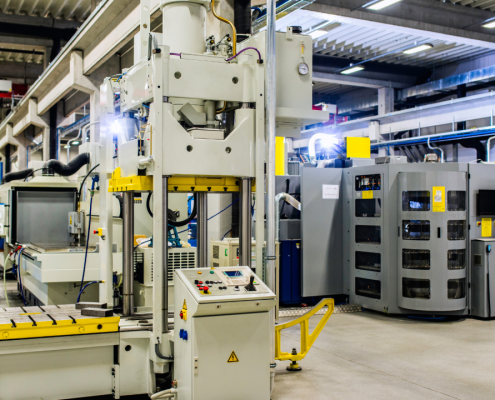
What is CNC Machining? A Beginner’s Guide
In modern manufacturing, machines do much more than just drill…