Tag Archive for: metal welding
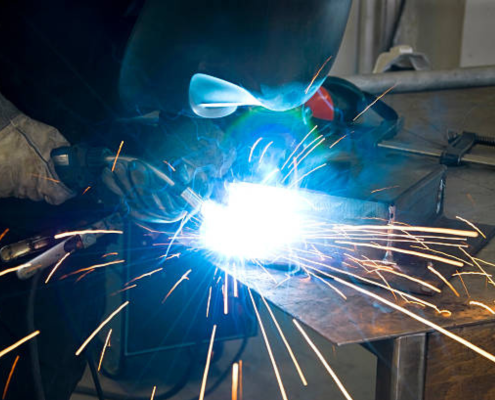
Metal Welding vs Soldering vs Brazing: What’s the Difference?
/
0 Comments
When it comes to joining metals or other materials in manufacturing…
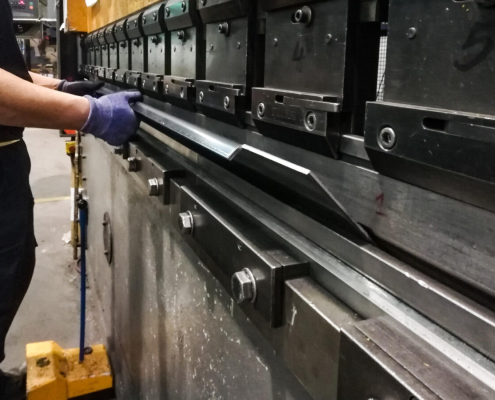
Metal Presswork or Fabrication? How to Choose for Your Next Project
When it comes to manufacturing custom metal parts, the decision…
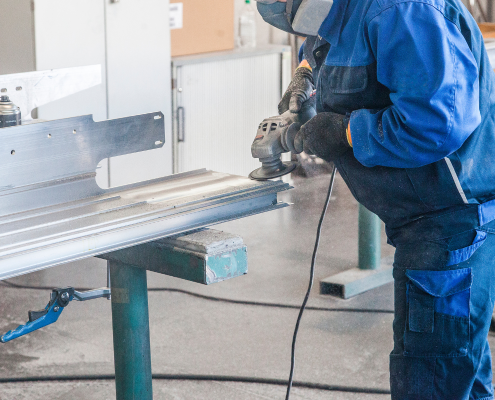
Metal Fabrication Methods Comparison : Choosing Between Welding, Presswork, and Machining
When working on a metal project, choosing the right fabrication…
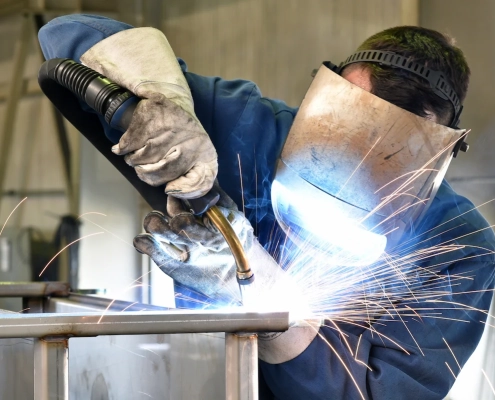
10 Common Metal Welding Defects and How to Avoid Them
Welding is a process used to join metal parts together. When…
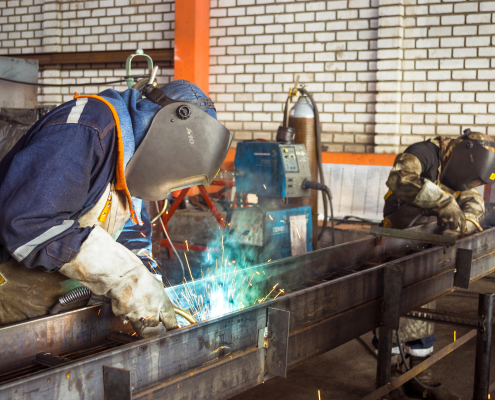
MIG vs TIG Welding: Which is Best for Your Project?
Welding is one of the most important processes in metal fabrication…
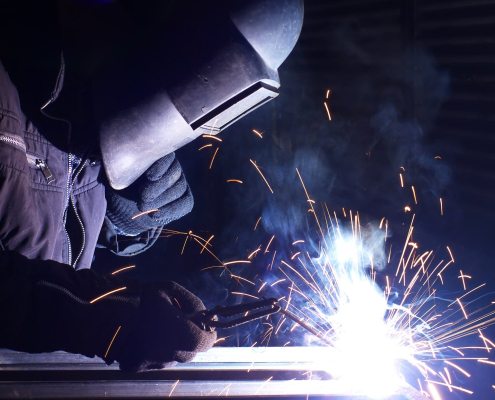
Different Types of Metal Welding and How They’re Used
Welding is one of the foundational processes in manufacturing…