Tag Archive for: metal fabrication
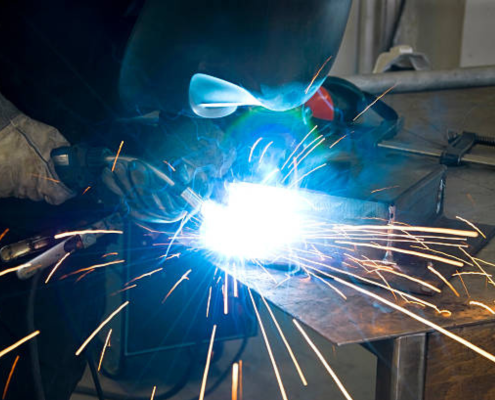
Metal Welding vs Soldering vs Brazing: What’s the Difference?
/
0 Comments
When it comes to joining metals or other materials in manufacturing…
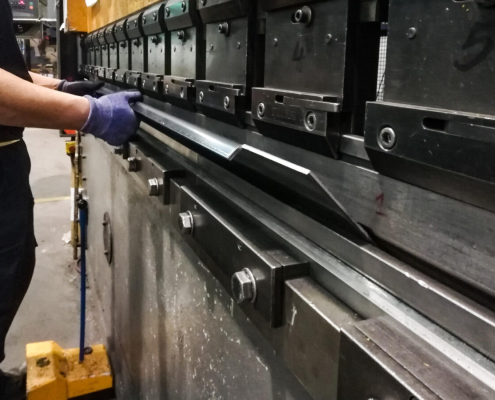
Metal Presswork or Fabrication? How to Choose for Your Next Project
When it comes to manufacturing custom metal parts, the decision…
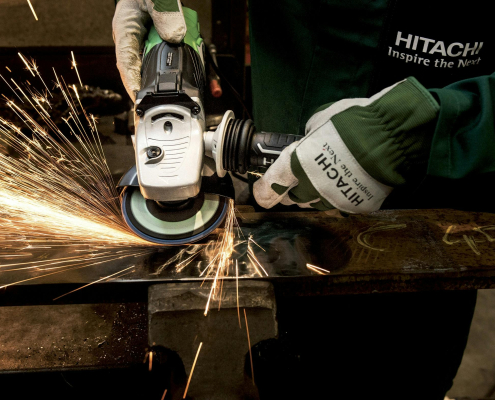
From Design to Delivery: The Complete Metal Presswork Process
In the world of manufacturing, precision and efficiency are crucial.…
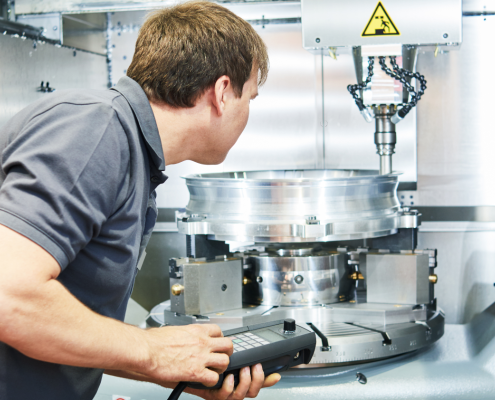
How Metal Presswork, Fabrication, and Machining Work Together in Manufacturing
Manufacturing is a highly complex process that requires a combination…
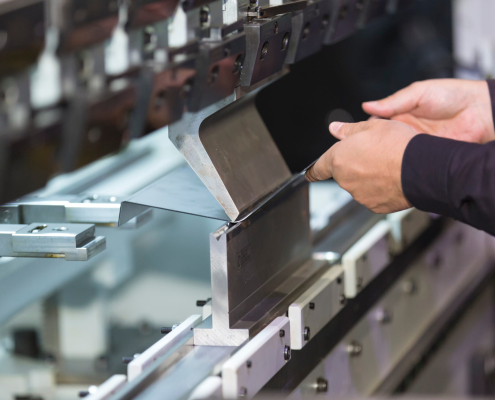
Metal Fabrication Guide: Custom Cut Sheet Processes, Applications, and Services
Custom sheet metal fabrication cutting is a fundamental aspect…
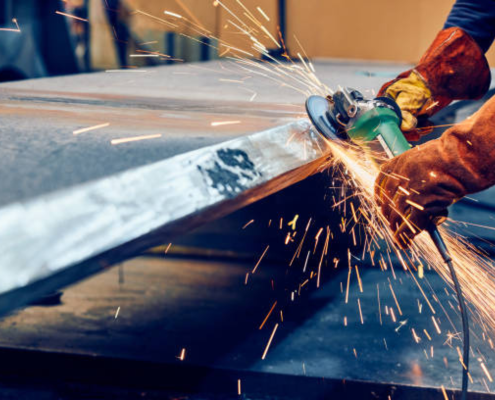
From Cutting to Forming: The Complete Guide to Modern Metalworking Methods
Modern metalworking is a fascinating and ever-evolving field…
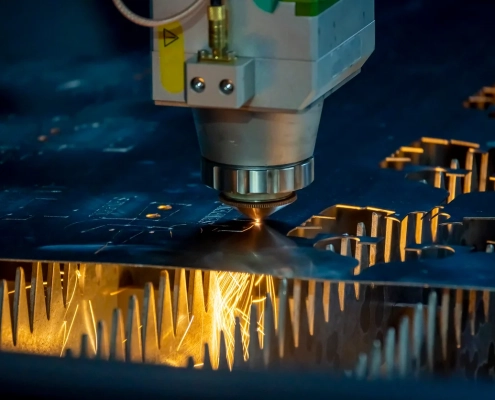
How to Get Accurate CNC, Laser Cutting, and Fabrication Quotes
When you’re undertaking a custom manufacturing project, whether…
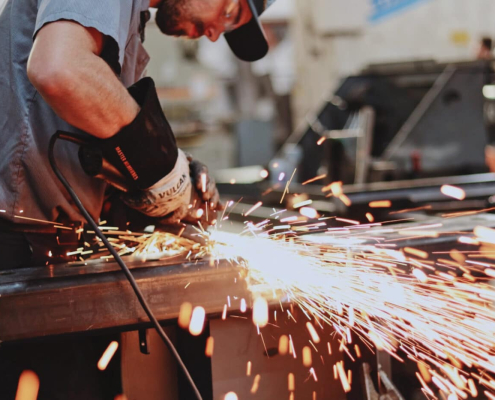
Custom vs Standard Metal Fabrication: What’s Best for Your Budget?
When starting a metal fabrication project, one of the first decisions…
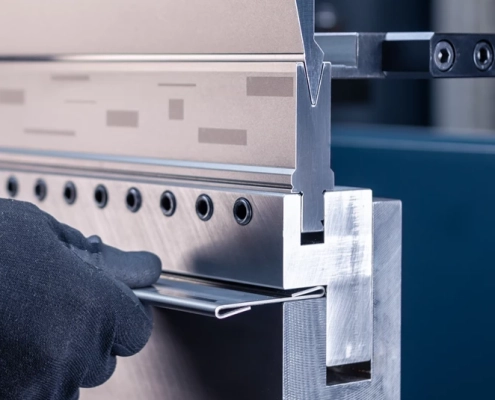
How to Choose the Right Metal Press Tooling for Your Metal Parts
In metal fabrication, precision and efficiency are key. One of…
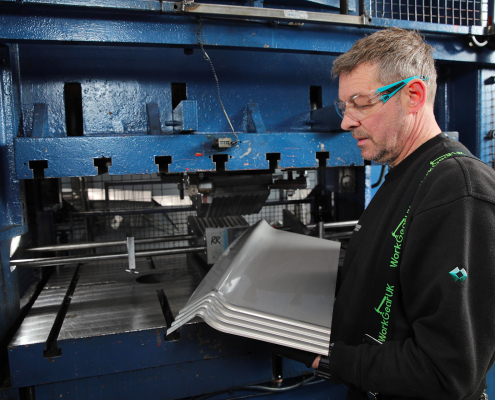
How to Choose the Best Metal Presswork Supplier for Your Business
If you’re working in manufacturing, product design, or engineering,…